◆設計では何を優先すればよいでしょうか?
◆はじめに
よく言われることは品質・コスト・納期の3つ。いわゆるQCDです。(Quality Cost Delivery)しかし実はQCDの前に隠れているものがあります。
それが【S】Safty、安全です。アスベストやPCBといった物質は、断熱性や絶縁性に優れた特性を示し、かつては多用されていました。しかし徐々に健康被害が明らかになり、今では使用が禁止されています。
材質だけでなく機能面でも、通常の使い方で怪我をするような製品であっては話になりません。
いくら便利で有益であったとしても人間に害を及ぼすものを作るわけにはいきません。安全であることが大前提になります。
そしてもう一つ、【E】Environment、環境です。冷蔵庫の冷媒として多用されていたフロンは今ではその使用だけではなく生産も規制されています。ところで一言でフロンと言っても複数の種類があります。
オゾン層破壊の原因とされてすでに全廃されたのはクロロフルオロカーボンズ(CFC)。
CFCの代替として利用されてきたのがオゾン層への影響が比較的少ないハイドロクロロフルオロカーボンズ(HCFC)。これは2020年中には生産全廃となる予定です。
さらなる代替としてハイドロフルオロカーボンズ(HFC)やパーフルオロカーボン(PFC)。
HFCやPFCはオゾン層を破壊しませんが一方で超強力な温暖化物質であり、CO2の温室効果の数千から1万倍程度の温室効果があります。このため、これらの物質の使用を規制する動きがあります。例えばHFCは、オゾン層を破壊する物質に関するモントリオール議定書に対して2016年にキガリ改正が採択されて2019年にその改正が発効されたことで、各国は今後30年で80%以上削減することを約束しました。
このような中で、設計者は安全性と環境性をどのように評価・担保するのか?
リスクアセスメントとライフサイクルアセスメントです。
今回はリスクアセスメントについてみていきます。
◆リスクアセスメント
最初にリスクとは「危害の発生確率およびその危害の程度の組み合わせ」と定義されています。つまりリスクは次の式で見積もることができます。
[リスク = 危害の発生確率 × 危害の程度]
次にリスクアセスメントには4つの手順があります。
1.危害の特定
2.リスクの見積もり
3.リスクの低減
4.リスクの再評価
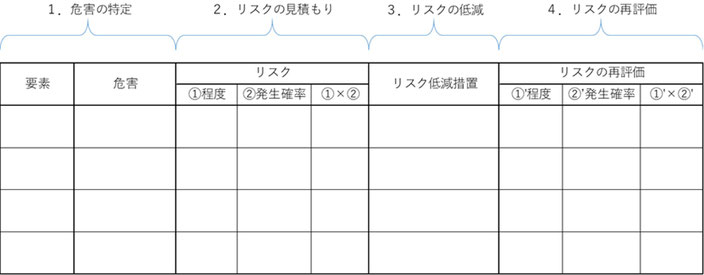
1.危害の特定
要素には2つの視点があります。
①製品の構成要素
例①:扇風機のファン、コンセントなど
②人の行動
例②:組み立てる、持ち運ぶなど。
それぞれの要素で発生し得る危害について書きだしていきます。
例①:ファンに手指が巻き込まれる。コンセントから漏電する。
例②:組立時に鋭利な部分で手指を切る。持ち運び時に滑って落とす。
2.リスクの見積もり
(1)危害の程度と発生確率をそれぞれ評価します。
[程度の評価例]
評価点 3
死亡や体の一部に永久的な損傷を及ぼす。
評価点 2
1か月未満の休養を必要とする怪我を生じる。
評価点 1
かすり傷程度のもの
[発生確率の評価例]
評価点 3
かなりの集中力をもって扱っても災害に繋がる。
評価点 2
うっかりで災害に繋がる。
評価点 1
意図的な行為で災害に繋がる。
*発生確率を評価するためには人の行動についての理解が必要です。人の行動は別途解説予定です。
(2)程度と発生確率の評価点を積算し、優先順位を3つに分けます。
優先順位Ⅲ 積算結果(9,6)
→すぐやる
優先順位Ⅱ 積算結果(4,3)
→計画的にやる
優先順位Ⅰ 積算結果(2,1)
→機をみてやる
3.リスクの低減
ISO12100あるいはJIS B 9700に出てくる3ステップメソッドに倣います。3ステップメソッドの詳細についてはそれぞれ4月13日以降、順次解説していく予定です。
[ステップ1]本質安全設計
①危険源の除去
②フール・プルーフ
③フェイル・セーフ
④冗長性
簡単に言うと、①危ないものを無くす②危ないことができないようにする③異常時は安全に停止させる④異常が起きても予備がある。
実は冗長性の上位概念にフォールトトレランス、異常があっても機能が働き続けるというものがあります。
[ステップ2]工学的処置
①安全防護によるリスクの低減、付加保護方策の実施。
※要するにカバーを付けることです。
[ステップ3]
①マニュアルやエラー/アラーム表示による注意喚起
※クレームの時に、「ここに書いてありますよ!」といえるように準備するという事です。
4.リスクの再評価
リスクの低減措置のあとで再度リスクを評価して低減措置の効果を確認します。もしまだ不十分であればさらなる低減措置を施して再々評価を行います。
◆おわりに
生産現場に協働ロボットを導入したい方へ。
ロボットメーカーから「協働ロボットです。人と同じ空間で作業が可能です。」と言われて鵜呑みにしてはいけません。ユーザーサイドでも必ずリスクアセスメントを行ってください。メーカーサイドでいくら安全に配慮をしても使い方次第では危険ですし、ユーザーサイドでどのような使い方をするかはメーカーサイドでは分からないからです。
確かに作業中の協働ロボットにぶつかっても痛くないです。おぉびっくりした!程度で済みます。しかし、そのロボットハンドにはんだごてを持っていたらどうでしょうか?火傷します。
パワーの弱いモーターを使っていたり衝突検知をして逃げてくれたりする協働ロボットですが、使い方次第で危険は生じます。
前のブログはストッパの設計です。
次のブログは3ステップメソッドについての予定です。
技術資料一覧はこちらから⇒「技術資料」
コメントをお書きください