ピック&プレイス動作を例にとります。
ピック&プレイス動作
図1に示すように、初期状態で原点にいる吸着パッドがA点で部品をとり(ピック)、B点に部品をおきます(プレイス)。その後、吸着パッドが原点復帰して終わりです。
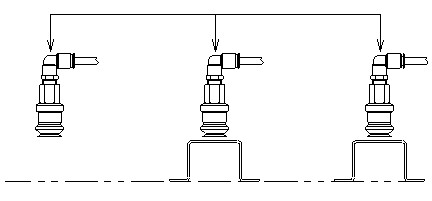
動作フローチャート
ピック&プレイスの動きをシンプルにフローチャートで書き表すと図2のようになります。
*A点、B点への移動は各工程動作の中に入っているものとします。つまり[部品吸着(A点)]の工程はA点に移動して吸着するものとします。
これでも動き自体は表現されています。ここで、仮に何らかの理由でしっかりと吸着ができていないときを考えると、このフローではしっかりと吸着ができていなくとも次のステップ、部品を置きにいってしまいます。
いわゆる空振りです。
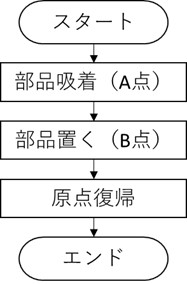
空振り対策フローチャート
機械に空振りをさせないために、図3に示すフローチャートのように吸着完了を確認するステップを1つ入れます。
シンプルなことですが、この1行があることでハードを設計する人間には「吸着を検知するためにここにセンサー(例えば図4に示すような真空スイッチなど)を入れる必要があります。」と共通認識できますし、ソフトを設計する人間には「ここで吸着を検知するので、それを確認してから次のステップに進むようプログラミングする必要があります。」と共通認識ができます。
吸着完了を確認してから次のステップに進むのなんて当たり前でしょう?!
いえ、当たり前ではありません。違うやり方も存在します。
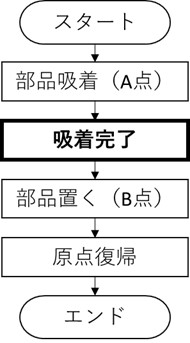
タイマーステップフローチャート
図4に示すように、吸着完了を確認するのではなく既定の秒数(ここでは1秒としています。)経過後に次のステップに進むというものです。何度かトライ&エラーを繰り返すことで「これだけの時間を待機させれば確実に吸着ができる」という秒数を確認して、設定します。
このやり方の利点はセンサーを付けなくてよい、ということが挙げられます。また時間を設定するので「サイクルタイムが確定する」という利点もあります。
ただしこのやり方は、対象の作業が「時間が経てば確実に完了する作業」ではない場合は効果がありません。
例えば吸着で言うと、機械の動きが速すぎて吸着の真空が完了する前に(しっかりと吸着される前に)次の動作に入ってしまうような場合は効果があります。
一方、「材料の高さがバラついて低いものが供給されて、そもそもパッドが届かない」という場合には効果が無く、空振りをしてしまいます。なおこの場合、吸着完了を確認するようにしているとだんまり停止が発生してしまいます。
タイマーでステップを進めるフローチャートを描くとハードの設計者にはセンサーは不要です。ソフトの設計者にはタイマーを入れる必要があります。と共通認識ができます。
ハード設計が先行してすすみ、センサーなどを含む構成がそこそこ固まってからソフト設計に入ることがあるかと思いますが、このようにフローチャートをまず作ってハード・ソフトそれぞれの設計者と共通認識をとることで同時に設計を進めることができます。
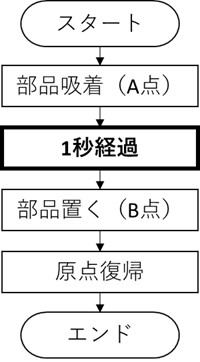
まとめ(比較)
図3のように吸着完了をセンサーなどで確認してから次のステップに進むフローでは空振りをしません。作業ごとの状態を確認し、その品質を作業ごとに保証するタイプと言えます。
一方、図4のようにタイマーでステップを進めるタイプは空振りをしても分かりません。作業ごとの品質を保証せず、機械の都合でものを作って最終的な検査などで品質を保証するタイプと言えます。
どちらが良いかはケースバイケースです。設計思想を明確にし、どちらにするかを決める必要があります。
本記事の途中でだんまり停止について言及していますが、このようなトラブル発生時はどのように対処するのか?ここを次回みていきたいと思います。
前のブログはアングルフレームの継ぎ目です。
次のブログはフローチャートで設計思想を表現しよう2です。
関連ブログ
コメントをお書きください