◆士業コラボで中小企業を応援!
◆士業コラボオンラインイベントについて
2020年4月29日に記念すべき第一回は新型コロナ支援策総ざらいを、続く5月4日の第二回では新型コロナ貸付、持続化給付金をテーマに士業コラボzoomオンラインイベントを開催し、それぞれ中小企業診断士、税理士の方から今の状況を生き延びるためにコロナ対策の様々な助成金や補助金、融資についてお話しがありました。
そして5月13日(水)18時から1時間、製造業向けに絞っての製造現場改善計画、要するに自動化のススメをお話しさせていただきましたので概要を書き留めておきます。
◆今こそ着手!アフターコロナに飛躍するための製造現場改善計画
上記タイトルで次の章立てで1時間お話ししました。
はじめに ビフォーコロナから続く世の中の動き
第一章 目指すべき姿
第二章 自動化の目的
第三章 現状把握とゴール設定をしよう⇒自動化レベル0~5について
・ビフォーコロナから続く世の中の動きというのはあくまで製造業に絞ったお話しです。
・ここで言う目指すべき姿は長期的な理想像ではなく、それを分解した1年後の目指す姿です。
・QCDは目的ではなく評価の指標です。
・何事も現状とゴールを明確にしないと始まりません。
◆ビフォーコロナから続く世の中の動き
要点は2つあります。
(1)2018年の白書に人材確保対策において最も重視している取組(現状と今後)のアンケートがあります。これによると現状の取組は新卒採用や中途採用など、人材確保を重視していることが分かります。一方で今後の取組としては自動機やロボットによる自動化やIT・・・AIによる合理化の取組を重視していることが分かります。
(2)2019年の白書に人材確保の状況のアンケートがあります。これによると人材確保の状況が「大きな課題となっており、ビジネスにも影響が出ている」と答えた企業が2016年22.8%⇒2018年35.7%、一方で「課題はない」と答えた企業が2016年19.2%⇒2018年5.2%と、とても悪化しています。
上記(1)(2)を合わせるとまずは人材を確保してから自動化や合理化への取組を行う姿勢がうかがえます。しかし人材確保が思うように進んでいない現状が見て取れます。
ここまでの話の詳細はブログ
「ものづくり白書の公開は5月下旬~6月初旬です。2」をご参照ください。
さてここで「人材確保対策において最も重視している取組(現状と今後)」のアンケートは実は大企業と中小企業とに分けた結果もありますので図1に示します。今後の取組として大企業は自動機やロボットによる自動化はほとんど伸びておらず、IT・・・AIによる合理化が大きく伸びています。一方で中小企業は自動機やロボットによる自動化が大きく伸びています。
ズバリ言ってしまえば大企業は資本力もあり、技術者もそろっている。技術者が足りなければ募集すればそれなりに集まる。という現実があり、すでに自動機やロボットによる自動化はある程度進んでいる。今後は次のステップである合理化に取り組みたい。という姿勢がうかがえます。実際に私自身、2016年2月にとある大企業に転職し在籍約2年の間に協働ロボットを使った自動組立ラインを構築しました。
コロナは関係なく、人材確保・育成の取組と自動化・合理化への取組は製造業において継続的に行われてきており、その結果は大企業と中小企業とで差があるのが現状です。この状況のまま進めば、自動化合理化に成功した企業とそもそも取り組めなかった企業との2極化がどんどん広がる未来が待っています。
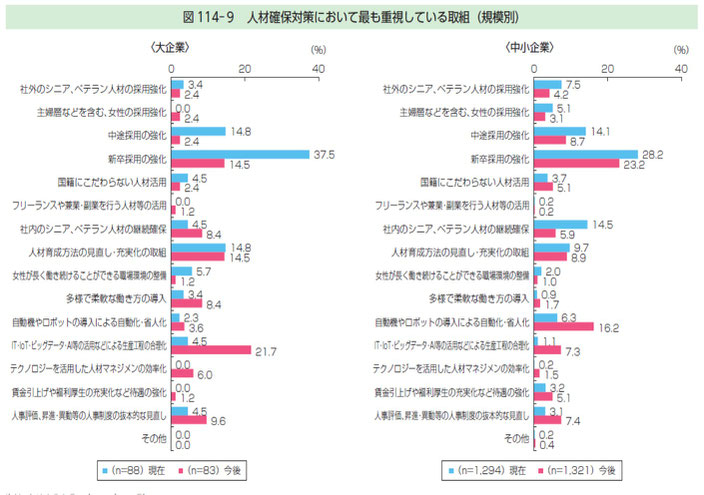
◆第一章 目指すべき姿
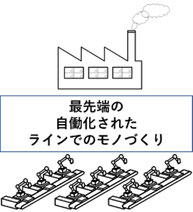
理想の状態は図2のような最先端の自働化されたラインでのモノづくりかもしれません。でもいきなりそれを目指そうとしても人手の問題、技術の問題、資金の問題、敷地の問題、など様々な問題に直面してしまい組織も人も身動きが取れなくなってしまいます。
余談で私も少しだけお手伝いしたことがあるのですが、中国では国が多額の補助金を出し指定地域を提供し新工場を建てて最新設備を導入する体制がありました。つまり土地と資金、加えて中国にはまだまだ人手がたくさんあります。とはいえ生産年齢人口は2015年ごろから減少に転じています。
では自動化が上手くいかなかった企業はどうなるのか?
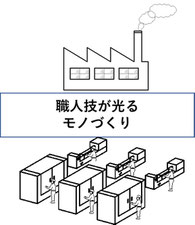
図3のように機械に替えることが出来ない作業、職人技が光る作業というのは大なり小なり必ず残ります。
このまま進めば自動化されたラインでのモノづくりor職人技が光るモノづくりの2極化がますます広がります。
どちらを目指してもいいとは思いますが、ゼロかイチか?やるかやらないか?という議論には違和感を覚えます。
間を取っていま職人さんがやっている10の作業のうち3つくらいは自動化できませんか?3つのうちまずは1つ着手してみませんか?
10のうち3つを自動化して職人と自動機が共存する現場を目指してみませんか?というのがこの章での私からの提言です。
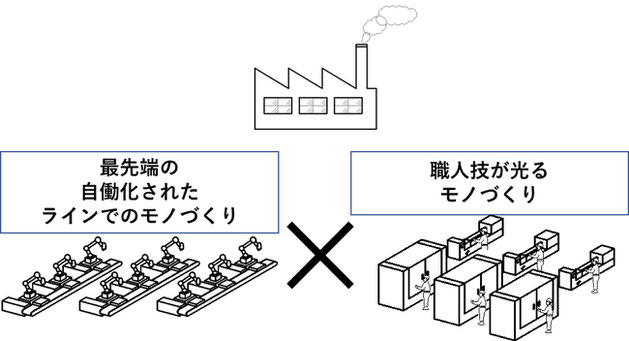
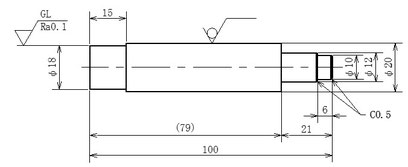
図5 軸の加工図面
図5に示すような軸を加工するときを考えてみます。
月に100本製作。1本当たり10分かかるとすると、1,000分≒16時間です。約2日間の作業になります。
私は加工の専門家ではありませんが、旋盤やフライス盤、ボール盤といった加工機を扱ったことはあります。設備を立上中に急ぎでセンサー追加したいのでセンサーブラケットが必要だとか、ドライバーのハウジングが自動作業中にワークと微妙に干渉するためちょっとだけ削りたいとか、穴位置が悪くいっそ長穴にしたいとかそういうときに自分で加工機に向かいました。私がこの軸を加工するとすれば旋盤を使って次の手順で作業を行います。
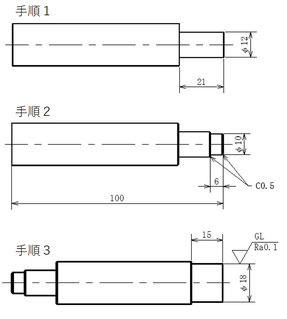
手順1
旋盤で部品をチャックしφ12長さ21の段付き部分を右側から加工する。
手順2
チャックはそのまま、φ10長さ6の段付き部分を右側から加工し、角部の面取りを行う。全長100mmで突っ切り。
手順3
ワークをひっくり返してチャックし直し。右側からφ18長さ15を加工した後、手仕上げを行う。(GL:ラッピング仕上げ)
一つの製品を作るにも複数の工程(手順)があります。この例では手順1,2はロボットに置き換えられるのではないでしょうか。ロボットが材料を取って旋盤にセットする。旋盤はいわゆるNC旋盤を使用し自動で段付き部を加工する。段付き部の加工が終わったらロボットが材料を回収し仕掛品として保管する。ロボットが1日作業を行い100本の仕掛品ができたら翌日に人が仕上げを行う。
いま人が行っている一連の作業のうち、一部でも自動化できる部分はあるのではないでしょうか?
10の作業のうち3つくらい自動化できそうな部分を挙げていただければ、どうやってやるか?ハウツーを私が一緒に考えさせていただきます。
◆第二章 自動化の目的
自動化に限らず、設備導入や現場改善を行う際の目的にはQCDを挙げることが多いかと思います。QCDは目的にしてはダメです。
自動化の目的は「人や国・地域に依存しない生産体制を構築すること」です。ここで言う人とは人の数。国・地域とは人件費の安い国や地域のことです。つまり安い人件費で人数がそろう国や地域に頼らない生産体制という事です。
QCDはその取組にメリットがあるかどうかを測る数値指標です。それぞれの数値は次の通りです。
(1)Quality:品質
自動化設備導入時の品質評価は「直行率」で行います。直行率とはその設備を使って製品を作った時の一発合格率になります。100個の製品を作った時に90個が一発合格だとすると合格率は90%になります。
ではこの直行率は実際に設備を導入してから製品を作ってみないと評価できないのか?というとそうでもありません。詳細は日刊工業新聞社さんの「機械設計」での連載に書きおろしていますが、統計学の知識を使えば事前にある程度の評価ができます。
(2)Cost:コスト
例えば生産用機械器具、金属加工機械製造設備の耐用年数は9年です。設備導入時にはこの耐用年数ではなく、その設備で製作予定の製品寿命を考慮します。おそらく耐用年数よりも短いと思います。
仮に設備が1800万円、製品寿命が3年間とするとコストは次のようになります。
1800万円÷3年間=年間当たりの設備コスト600万円
自動化≠無人化です。設備本体のコストに加えて人件費を考える必要があります。この人件費は設備のメンテナンスをするための人件費になります。1日当たり1時間程度メンテナンスをする必要性を想定すればそれ相応のコストが必要になります。
仮に作業者の人件費が年間一人当たり250万円、設備導入をしない場合は3人作業とすると年間人件費は750万円となり、設備単体のコストはゆうりになります。
またこの場合の3人というのは作業者がパートの方だったりすると固定の人員ではなく3人1チームが入れ替わりで作業を担うこともあります。その場合は6人あるいは9人の作業者を確保する必要があります。
(3)Delivary:デリバリー
設備導入時のデリバリー評価は「サイクルタイム」と「リードタイム」で行います。複数工程を経て製品が完成される場合、1つの工程を完了する時間をサイクルタイム、工程の最初から最後までを経て1つの製品が完成するまでの時間をリードタイムと言います。サイクルタイムとリードタイムから設備の生産能力を確認します。サイクルタイムの詳細はブログ「サイクルタイム」をご参照ください。
◆第三章 現状把握とゴール設定をしよう 自動化レベル0~5について
自動化レベルについてはブログ「工場自動化レベル」をご参照ください。第一章、第二章から現場作業10のうち3つ狙いを定め、自動化の目的を確認したら3つの狙いの現状把握を行い、ゴールを設定します。そのための自動化レベルです。
ゴールを設定したら各レベルに必要な知識・技術を確認してください。
レベル2 機械要素、設備
レベル3 機械要素、設備+PLC(制御機器)
レベル4 IoT、センシング
レベル5 統計解析、AI
第一章、第二章、第三章を通じて、狙い・目的・現状とゴールを確認できたら構想を練っていきます。自動化設備の構想を練るにあたって重要な項目は2点です。
1.設備動作のフローチャートをしっかりと書くこと。
2.設備そのものの品質=設備信頼性を評価しておくこと
◆おわりに
自動化できない理由は様々なものがあります。
できない理由1.人がいない!
できない理由2.うちは○○だから無理!!
できない理由3.何から始めればよいのか分からない!!!
できない理由はすべて×をして、できる理由に変えます。

できる理由1.今が一番人手がある。(将来的に増える見込みは薄い)
できる理由2.狙いを絞ってできるところから創意工夫で挑戦する。
できる理由3.自動化レベルから現状とゴールを明確にする。
ご連絡頂ければどうやってやればいいか?zoomなどを使ったオンラインミーティングで一緒に考えさせていだだきます。
前のブログは前のブログはものづくり白書の公開は5月下旬~6月初旬です。2
次のブログはボルトとボルトの間です。
コメントをお書きください