関連ブログ [現場で取得すべき4種類のデータ]
◆保全=メンテナンス=調整作業+点検作業
◆保全の定義と4つの保全活動
傾向管理をして不良の芽をつぶそう!よく聞きますね。
◆保全ってなんやねん?!
不良が出る前に手入れを行い、不良ゼロを達成しようというものです。
さてここで保全活動とは健「全」な状態を「保」つ活動のことを言います。ここではもう少しわかりやすくかみ砕いて、設備の「点検」と「調整」を合わせた活動のことと定義します。
では点検と調整とは何でしょうか?
点検 : 設備が異常な状態になっていないかを確認し修正する行為のこと。
例えば設備の証明が暗くなってきた、ボルトが緩んでいる、○○が摩耗している、ゴムがへたったなどの異常が発生していないかを確認し、異常が認められたら修正します。
このように「設備を正しい状態に保つ行為」をここでは点検と言います。
調整 : 設計トルクが8.4±0.5 N・mだったので機械の設定トルク8.4N・mで締め付けたボルトが、実トルクを測定したところ7.93N・mでした。思ったより低かったので「設定トルクを9.0N・m」に変えてねじ締めしたところ、実トルクが8.42N・mと設計トルクにより近い値となりました。
このように得られた結果から設定トルクの値を変更する行為をここでは調整と言います。
保全 : メンテナンスと同じ。保全=点検+調整
◆保全って4つあるよ。
1.保全予防
~~越えられない壁1~~
2.予防保全
・時間計画保全・・・経時保全と定時保全
~~越えられない壁2~~
3.事後保全
4.改良保全
◆保全予防、設計段階で保全をしっかりと考慮する。
1.保全予防
設計段階で保全に関する事項を考慮した製品にする方法。
駆動機器を安全対策のためにカバーで完全に覆ってしまうとメンテができない!メンテ用の窓を設けた設計にするなど、保全を考慮して設計しないと当然のようにクレームがきます。
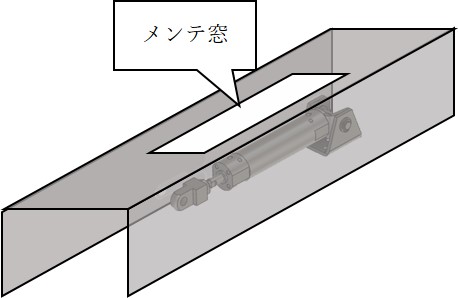
保全の方法や、日ごと週ごとなど頻度をしっかりと設計しましょう。頻度を設計するためには統計の知識を応用する必要があります。
このことを理解して設計すればゼロディフェクトを達成する設備が設計できます。
込み入った話になりますので、ここはセミナーで解説しています。
◆設備トラブルを起こさない。予防保全活動
2.予防保全
保全を語るうえで最重要項目がここです。
予防保全には(1)「時間計画保全」と(2)「状態監視保全」があります。
さらに(1)時間計画保全には①「経時保全」と②「定期保全」があります。
(1)時間計画保全
①設備、機器の動作があらかじめ定めた時間に達したら行う保全、というか交換。
Oリングやヤーンパッキンなど、パッキンの累積使用時間が一定時間に達したら交換。
リニアガイドの駆動距離が100kmに達したら交換。
②あらかじめ定められた期間に達すると問答無用で保全、と言うか交換。
月例点検、定修工事、など。まだ使えるかもだけど交換。
(2)状態監視保全
一般的には、設備の状態を何かしらのセンサでモニターして、異常を検知したり、異常になりそうな予兆を検知したりする行為を言います。
例えば振動を検知するためにボルトをピエゾボルトに変更すると、設備が発する振動を検知できます。例えばボール盤で穴あけをするときに、異物(ゴミや切りくず)がドリルに巻き込まれた場合、設備は異常な振動発生します。検知する仕組みが無ければそのまま穴あけ加工をして、場合によってはドリルが折れたり加工不良が発生したりします。
振動を検知するピエゾボルトを使用するとこのような異常が発生した瞬間に発見することができます。
もう一つ、異なる方法で設備の異常を発見することができます。
設備の信頼度が分かっている場合。例えば信頼度が99.9%の場合、1,000回に1回不良が出ます。
このとき仮に1日の生産量が1,000個だった場合。
・1日の間に「2回」不良を出す確率は百万分の1です。
・1日の間に「3回」不良を出す確率は10億分の1です。
1日の間に2回不良を出した場合、それは設備に何かしらの異常が出ている、例えばどこかのボルトが緩んでいる、位置決めブロックが摩耗して位置決め位置がずれているなどの異常が発生している可能性が高いです。
点検と調整=保全を行いましょう。
不良の発生率をカウントするだけでも状態監視はできます。
コメントをお書きください